Introduction
Modern infrastructure rely heavily on remote control cabinets. You’ll find them placed along pipelines, beside railway signals, or inside of solar and irrigation systems. These cabinets act as the operational nerve centers—they manage automation, collect data, enable communications, and also distributes power.
But harsh and remote environments often challenge these systems. Grid power might fail or not exist, technician visits takes time and cost money, and power outages can shut things down entirely.
So in these demanding conditions, you should use a reliable and maintenance-free backup power. Sodium-ion batteries more and more meet this need. They offers chemical safety, long lifespan, strong performance in harsh environments, and smart diagnostics—features which older battery types often struggle with.
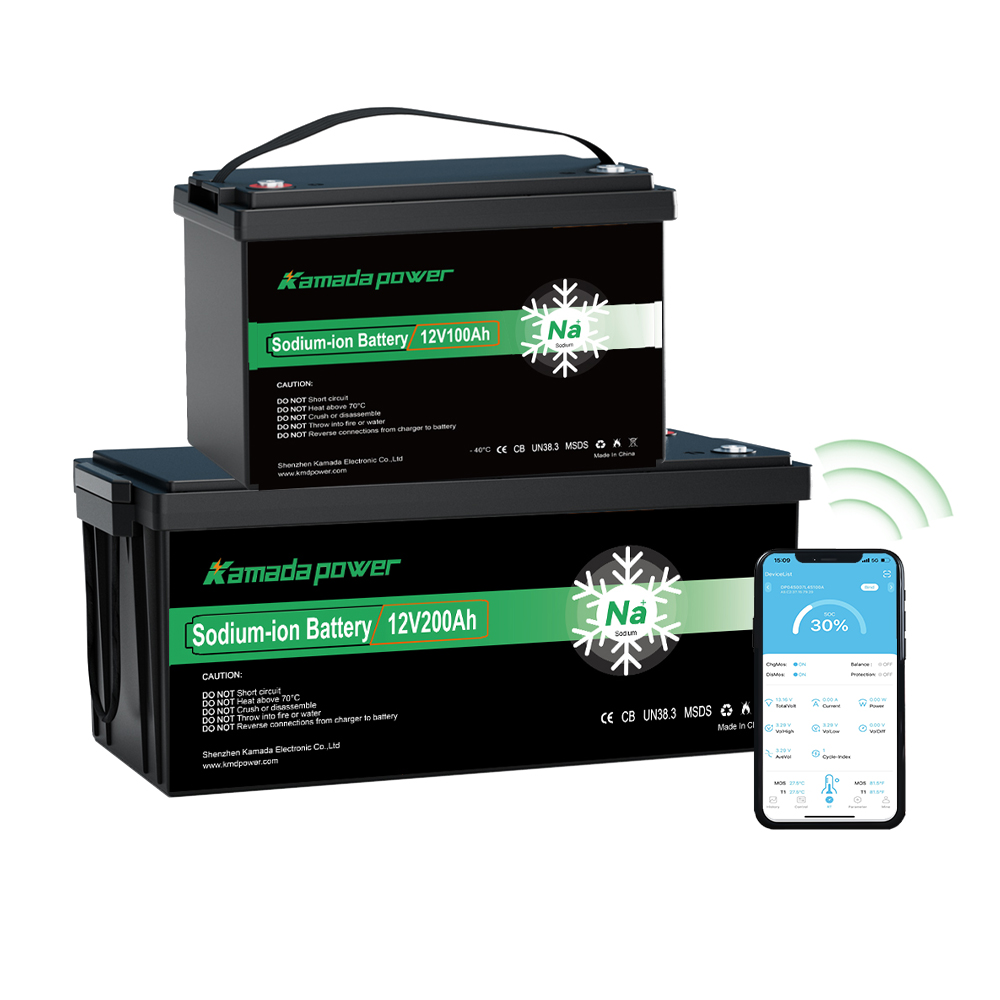
12v 100ah sodium ion battery
What Are Remote Control Cabinets and Where Are They Used?
You can consider remote control cabinets—sometimes called Remote Terminal Units (RTUs) or edge enclosures—as strong and weatherproof boxes that keeps automation, communication, and power devices protected at unattended sites. They forms the backbone of many infrastructures by enabling real-time control and link with central systems.
These units often includes PLCs, RTUs, modems, sensors, surge protectors, and backup batteries. Designers should plan them for harsh weather, variable loads, and long time between service.
Industry-Specific Applications and Technical Load Profiles
1. Oil & Gas Pipelines
- Typical Equipment: RTUs connect to flow and pressure sensors, valve actuators, modems, and arrestors.
- Electrical Load: Continuous load draws 15–25 watts; peaks reach up to 40 watts when valves actuate or data is sent.
- Environmental Conditions: Outdoor setups deals with dust, rain, corrosion, and temperatures from -20°C to +50°C.
- Operational Challenges: You might not service for months; batteries need to offer 72+ hours autonomy with low solar input.
- Battery Requirements: Provide steady voltage, remote diagnostics, and last long calendar life to reduce replacements.
2. Railway Signal and Switch Control Cabinets
- Typical Equipment: Controllers, motor drivers, repeaters.
- Electrical Load: Around 10 watts base, but surges over 50 amps occurs when switches activate.
- Environmental Conditions: Trackside locations are exposed with wide temperatures, dust, and vibration.
- Operational Challenges: Power interruptions not acceptable. Batteries need handle cold-weather pulses.
- Battery Requirements: High-rate discharge, operate through extreme temperature, and not fade at cold.
3. Water and Wastewater Utilities
- Typical Equipment: SCADA units, pump relays, level sensors, and radios.
- Electrical Load: 10–30 watts, changing during pump cycles.
- Environmental Conditions: Sometimes indoor but with humidity and even flooding risks.
- Operational Challenges: Equipment should work during outages and withstand moisture.
- Battery Requirements: Must be IP66 or better, long runtime, and chemistry that won’t degrade in wet.
4. Agriculture — Irrigation and Fertilizer Automation Cabinets
- Typical Equipment: Soil sensors, telemetry devices, PLCs, pump starters.
- Electrical Load: Most consume 5–15 watts; pumps causes surge.
- Environmental Conditions: Remote fields with heat, dust, and off-grid locations.
- Operational Challenges: With rare maintenance, reliability is must.
- Battery Requirements: Tolerate high heat, deep discharge, and monitor remotely.
5. Renewable Energy Microgrids and Edge Inverter Cabinets
- Typical Equipment: Inverter controllers, gateways, BMS interfaces.
- Electrical Load: Load varies; controllers use around 10–30 watts.
- Environmental Conditions: Exposed rooftop or ground with solar radiation and big temperature swings.
- Operational Challenges: Power quality should be consistent, integration smooth, and no frequent site visits.
- Battery Requirements: Must be safe chemistry, offer real-time diagnostics, and backup seamlessly.
This breakdown shows clearly how applications of control cabinets varies—and why you should match battery solutions to meet those tough requirements.
Why Traditional Battery Systems Fall Short
For many years, teams used lead-acid and lithium-ion batteries in these cabinets. But now these solutions shows their weaknesses:
- High Maintenance: You need to add water, clean terminals, and keep checking on them. Even lithium-ion systems need diagnostics.
- Environmental Struggles: Extreme hot or cold reduces performance. NMC lithium-ion often lose capacity in freezing.
- No Built-In Monitoring: Failures comes unexpectedly due to no remote visibility.
- Safety Concerns: Lithium-ion has risks of fire and thermal runaway. In remote areas, that’s a big concern.
These limitations means more costs, too much servicing, and outages that you can’t afford.
The Sodium-Ion Advantage: Purpose-Built for Edge Reliability
Sodium-ion batteries addresses those problems. They deliver long-term reliability for edge site backup power.
1. Superior Safety and Stability
They use non-flammable electrolytes and stable components like hard carbon and Prussian white. Because of that, the fire risk stays very low—even where wildfires might occur.
2. Maintenance-Free Longevity
You don’t need to water, balance, or cool them. Sodium-ion batteries provide 4,000+ cycles with little degradation. That equals to 8–10 years field life and big savings in cost.
At -20°C, they still retain over 90% of capacity. Compared with some lithium chemistries, sodium-ion batteries works better in cold conditions.
4. Integrated Smart Battery Management Systems
Modern sodium-ion packs includes BMS with RS485, CAN, and Modbus. They lets you monitor remotely, detect problems, and connect into SCADA/PLC for predictive repair.
Designing a Zero-Touch Backup Power System: Three Core Principles
To build a backup system that doesn’t require much hands-on, you should follow these three principles:
Principle 1: Self-Powered
Use solar or renewable energy to keep charging always. This lets systems run even in cloudy days for weeks.
Principle 2: Self-Protected
You add overvoltage, short-circuit, and other protections. The BMS will auto-handle those protections.
Principle 3: Self-Diagnosed
The system must tells you its status, faults, and health without someone to visit. This allows predictive fixes.
Recommended Configuration for Remote Control Cabinets
Component | Specification | Benefits |
---|
Battery | 12V 100Ah Sodium-Ion | Safe, compact, long-life |
Enclosure | IP65 or NEMA 4X Rated | Dustproof and weather-protected |
Communication | RS485 / CAN (Modbus) | Integrates smoothly with control systems |
Operating Temperature | -40°C to +70°C | Suitable for most locations |
Mounting | Floor or cabinet-internal | Matches standard cabinet footprints |
You could also request custom setups to suit your project’s needs.
FAQ
Q1: What is typical lifespan and cycles of sodium-ion batteries?
A: You’ll usually get 8–10 years of use and 4,000+ full cycles while capacity stays strong.
Q2: Can these batteries work with existing SCADA and PLC systems?
A: Yes, their BMS supports Modbus, CAN, and RS485—easy to plug into your platform.
Q3: Is the total cost better than lithium or lead-acid?
A: You pay a little more up front, but the long service life and lower maintenance saves more over time—usually in about 3–4 years.
Q4: Can they handle extreme weather?
A: Yes. These batteries perform well from -20°C to +55°C, even better than many lithium-ion cells.
Conclusion
Remote control cabinets must operate 24/7 with high reliability. Sodium-ion batteries gives you that reliability. You gain safety, hands-free operation, strong environmental tolerance, and smart diagnostics.
When you switch to sodium-ion solutions, you reduce downtime, save maintenance cost, and keeps your critical systems running—today and also in the future.
If you want to explore a custom sodium-ion battery solution or thinking about upgrading your cabinet systems, just reach out to our team for a consult.