Introducere
A Sealed Fanless 48V Sodium ion Battery Solution for Extreme Heat.For every field engineer responsible for maintaining telecom sites across the Middle East,We talk endlessly about the blistering heat, with ambient temperatures soaring past 45°C. We design complex, powerful HVAC systems to combat it. But for the teams on the ground, the most relentless, most frustrating adversary isn’t the heat itself. It’s the dust.
Fine as powder, carried on the Khamsin winds, this dust is an insidious infiltrator. It finds its way into every crevice, every intake, and most critically, it chokes the very lifeblood of your site’s reliability: the cooling system for your backup batteries. For engineers, the most frequent and tiresome task isn’t replacing a battery; it’s the bi-weekly, thankless chore of climbing a tower or driving to a remote shelter to clean or replace a filter that was pristine just days ago.
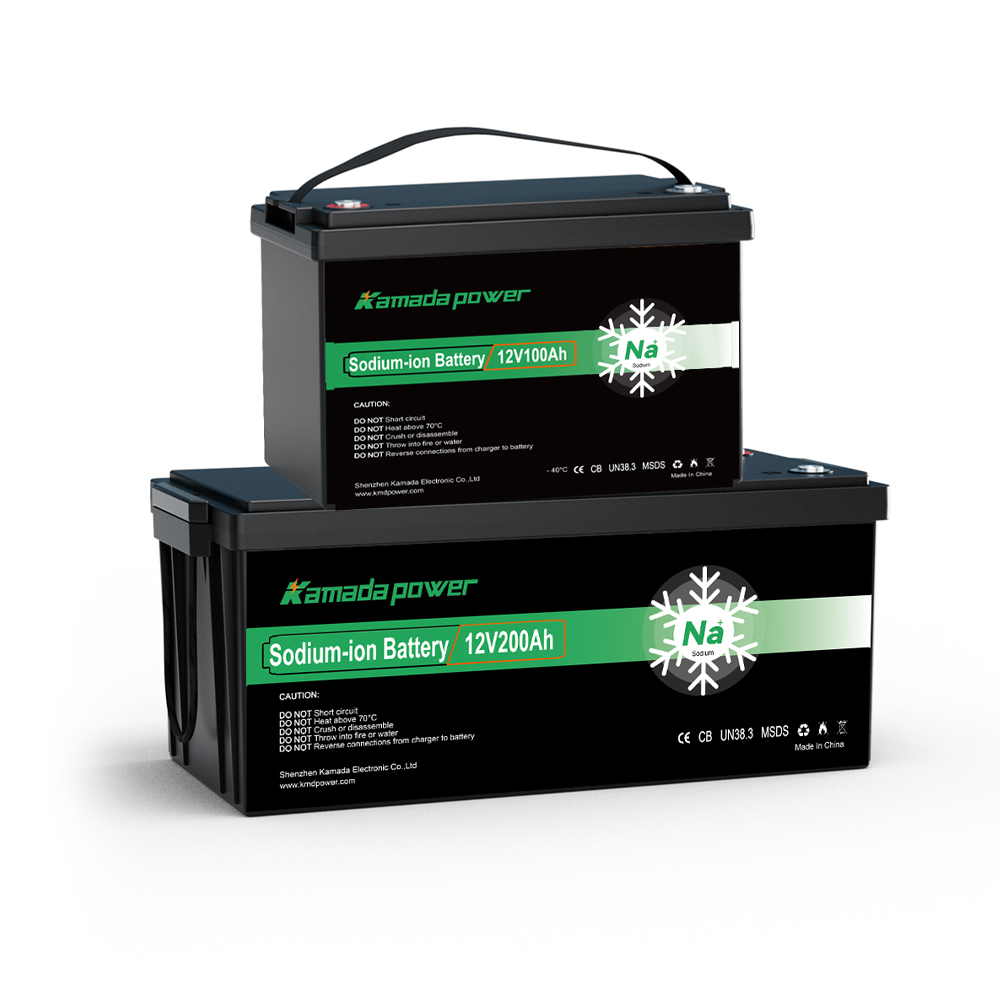
baterie kamada power 12v 100ah sodiu ion
This constant battle isn’t just a maintenance headache. It’s a critical vulnerability that silently sets off a chain reaction, leading to network downtime and astronomical operational costs. But what if you could design a power backup system that didn’t need to breathe? What if you could build a truly “dust-proof” power plant for your edge sites? This isn’t a futuristic dream; it’s a new reality enabled by a fundamental shift in battery chemistry and system design.
How Dust Silently Kills Your Network Reliability
The problem with dust is that its impact isn’t immediate; it’s a slow, creeping assassin that kills your network through a predictable and devastating domino effect. Understanding this chain reaction is crucial for any operations manager looking to improve network uptime and reduce OPEX.
The Domino Effect: A Vicious Cycle
- Dust Infiltration & Clogging: The journey begins as fine desert sand is pulled into the HVAC unit’s intake. It rapidly clogs the air filter, a component designed to be the first line of defense.
- Reduced Cooling Efficiency: With the filter blocked, airflow across the condenser and evaporator coils is drastically reduced. The HVAC unit must now work much harder, running for longer periods to achieve the same cooling effect. Its efficiency plummets.
- HVAC Overload & Failure: This constant state of overwork puts immense strain on the compressor and fan motors. The system overheats, leading to premature component failure and a complete shutdown of the cooling system.
- Skyrocketing Cabinet Temperatures: Once the AC fails, a sun-baked telecom cabinet in the desert becomes an oven. Internal temperatures can quickly surge from a controlled 25°C to a destructive 60°C, 70°C, or even higher.
- Accelerated Battery Degradation: This is where the backup power system enters a critical state. For every 10°C increase above their optimal operating temperature, the life of a traditional VRLA lead-acid or even a standard LiFePO4 battery is effectively cut in half. At 70°C, a battery designed to last for years might be permanently damaged in a matter of hours.
- Catastrophic Failure & Network Downtime: The battery, weakened and damaged by the extreme heat, fails to provide the required backup power during the next grid outage. The result: a dead site, dropped calls, lost data, and furious customers.
The Hidden Cost: A Drain on Your OPEX
This domino effect translates directly into tangible, recurring costs that bleed your operational budget dry:
- Labor & Transportation: The bi-weekly or monthly “truck roll” to remote sites just to clean or replace a $10 filter costs hundreds of dollars in fuel, vehicle wear, and, most importantly, the valuable time of skilled technicians.
- HVAC Energy Consumption: A clogged system runs inefficiently, consuming significantly more electricity. In a region where cooling can account for up to 50% of a site’s energy bill, this inefficiency directly inflates your utility costs.
- Premature Asset Replacement: The constant strain leads to more frequent HVAC and battery replacements, turning what should be a long-term capital investment into a recurring operational expense.
The traditional approach of fighting dust with more filters and more frequent maintenance is a losing battle. The only way to win is to change the rules of the game entirely.
Designing a System That Breathes No Air: The Fanless Advantage
The solution is deceptively simple: if your system doesn’t need to inhale air to stay cool, it can’t be choked by dust. The challenge, historically, has been that batteries—especially when charging and discharging—generate heat. Getting rid of this heat has always required active air cooling.
This is where the unique properties of Sodium-Ion (Na-ion) battery technology, combined with smart system design, create a paradigm shift.
Low Heat Generation: The Foundation of Fanless Design
The amount of heat a battery generates is largely a function of its internal resistance. The higher the resistance, the more energy is wasted as heat during operation (a phenomenon known as joule heating).
Modern Sodium-Ion cells are engineered for exceptionally high round-trip efficiency (often >92%) and feature very low internal resistance. This means that during both charging and discharging, significantly less energy is converted into waste heat compared to many other battery chemistries. This inherent high efficiency is the cornerstone of a fanless design; a battery that produces less heat requires less effort to cool.
The Power of Modularity: Building a 48V System with 4x 12V 100Ah Sodium ion battery
Instead of a single, large, monolithic 48V battery pack, our solution utilizes a modular approach: four individual 12V 100Ah Sodium-Ion battery connected in series. This isn’t just for electrical convenience; it’s a critical thermal design strategy.
By arranging the four modules with a calculated air gap between them, we maximize the available surface area for heat dissipation. This allows the system to cool itself passively through two natural processes:
- Natural Convection: The minimal heat generated by the blocks warms the air immediately surrounding them. This warm air rises, drawing cooler, denser air in from below, creating a slow, continuous, and silent air-cooling cycle within the cabinet, without any fans.
- Thermal Radiation: The surfaces of the battery blocks radiate heat away to the cooler interior walls of the enclosure.
This modular, passive cooling design is only possible because the foundational heat generation of the Na-ion cells is so low.
The Sealed Enclosure: The Ultimate Fortress Against Dust
Since the baterie cu ioni de sodiu system no longer relies on external air for cooling, we can take the final, revolutionary step: place the entire 48V system inside a sealed, non-vented enclosure, often with an IP65 rating or higher.
An IP65 rating signifies that the enclosure is completely dust-tight and protected against water jets from any direction. For a telecom site in the Middle East, this means:
- Zero Dust Ingress: No sand, dust, or humidity can enter the battery compartment.
- No Filters to Clog: The concept of a filter becomes obsolete.
- No Fans to Fail: The most common mechanical failure point in a cooling system is eliminated.
The battery system now exists in its own pristine, isolated micro-environment, completely immune to the harsh conditions outside. It has become a true “dust-proof power plant.”
From “Bi-Weekly Cleaning” to “Annual Inspection”: A New Maintenance Schedule
This shift in system architecture completely revolutionizes the maintenance schedule and philosophy for your remote sites. The contrast is stark.
(A side-by-side comparison table)
Sarcina de întreținere | Traditional System (VRLA/Li-ion with HVAC) | Sealed Sodium-Ion System |
---|
Filter Cleaning/Replacement | Bi-Weekly / Monthly | Eliminated |
Fan Inspection & Cleaning | Trimestrial | Eliminated |
Coolant/Refrigerant Check | Annually | Eliminated |
Battery Terminal Check | Annually (for VRLA) | Minimal (Sealed Terminals) |
Manual Battery Health Check | Quarterly / Annually | Replaced by Remote Monitoring |
Primary Maintenance Activity | Reactive & Physical: Constant cleaning and component checks. | Proactive & Digital: Remote data monitoring via BMS. |
Required Site Visit Frequency | ~12-24 times per year | ~1-2 times per year (for general site inspection) |
The paradigm shifts from a schedule of frequent, reactive, and physically demanding chores to one of proactive, remote monitoring. The only required site visits are for broader site integrity checks, not for tending to the battery’s life-support system. This translates into a 90% or greater reduction in maintenance-related truck rolls, freeing up your skilled engineers to focus on network expansion and optimization, rather than janitorial duties.
Concluzie
For decades, telecom operators in the Middle East have been locked in an expensive, unwinnable war against dust. We built powerful air conditioners, only to have them choked into submission. We scheduled endless maintenance, only to see our OPEX budgets spiral.
The sealed, fanless 48V Sodium-Ion system offers a path to peace. By fundamentally re-engineering the relationship between the battery and its environment, we can finally build a backup power system that is not just tolerant of the desert, but truly immune to its most persistent threat.
It’s time to stop cleaning filters and start building a more resilient, reliable, and profitable network. Let the desert winds blow; your power plant won’t even notice.
Ready to design a truly maintenance-free power system for your most challenging sites? Contactați-ne pentru o customized sodium battery solution from our team of battery experts.